
26 Sep. Integrierte Sensorik: Der nächste Schritt beim 3-D-Druck
Derzeit werden Sensoren in den meisten Anwendungen manuell auf die Oberflächen von Bauteilen angebracht. Mit einem neuen Verfahren, das Forschenden des Fraunhofer-Instituts für Lasertechnik ILT entwickelt haben, lassen sich Sensoren direkt in die Bauteile integrieren. Dadurch können wichtige Kenndaten über die Belastung innerhalb des Bauteils gesammelt werden. Samuel Moritz Fink, Gruppenleiter Dünnschichtverfahren am Fraunhofer ILT, sagt dazu: „Das manuelle Aufbringen von Sensoren ist in vielen Fällen zu ungenau und nicht reproduzierbar.“ Zudem fordern die Anwender zunehmend automatisierbare Prozesse, erklärt Fink den Entwicklungsansatz.
Erster Prototyp: Kraftsensor
Auf dem Fraunhofer-Gemeinschaftsstand der Formnext vom 7. bis zum 10. November 2023 in Frankfurt am Main wird beispielsweise ein PKW Querlenker mit additiv gefertigtem Sensor gezeigt. „Der Kraftsensor, den wir auf den Querlenker gedruckt haben, ist inklusive Isolations- und Schutzschicht sowie Anschlüsse nicht einmal 200 µm dick“, erklärt Fink. „Damit lassen sich die wirkenden Kräfte im Einsatz zu jedem beliebigen Zeitpunkt bestimmen.“ Diesen Prototyp haben die Fraunhofer-Forschenden für den Rennsport entwickelt. Der Sensor misst kontinuierlich die Kraftänderung etwa bei Kurvenfahrt und warnt vor Defekten, bevor sie entstehen.
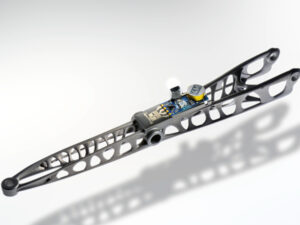
Der PKW-Querlenker mit aufgedrucktem Kraftsensor liefert zu jedem beliebigen Zeitpunkt die im Einsatz wirkenden Kräfte und registriert kleinste Risse, die auftreten, bevor ein Defekt entsteht. Bild: Fraunhofer ILT
Neben einem Kraftsensor sollen sich auch andere Sensoren aufbringen lassen, etwa zum Erfassen von Temperatur, Vibrationen oder Schall, Druck oder Beschleunigung, Licht, Spannung, aber auch für die Bestimmung unterschiedlicher Gase und Flüssigkeiten. Spezielle Kunststoffe für die Isolations- und Schutzschichten sollen Temperaturen von bis zu 300 °C standhalten. Das Anwendungsspektrum dieses Verfahrens sei laut den Forschenden immens, vor allem, weil es geeignete Echtzeitdaten für Predictive Maintenance liefert: „Damit lassen sich beispielsweise Batteriezellen einzeln überwachen, Wartungsintervalle bei Offshore-Windkraftanlagen optimieren oder Prozesse im Maschinen- und Anlagenbau verbessern“, so Fink weiter.
Herstellung in mehreren Stufen
Mithilfe von 3-D-Strukturdruck wie dem Verfahren des Laser Powder Bed Fusion (LPBF) können die gedruckten Sensoren direkt in die Bauteile integriert werden, während sie entstehen. Die Technologie demonstrieren die Fraunhofer-Forschenden ebenfalls auf der Formnext am Beispiel eines additiv gefertigten Fräskopfs. Der Strukturdruckprozess mittels LPBF wird unterbrochen, um Dehnungsmessstreifen mithilfe eines digitalen Funktionsdruckverfahrens und laserbasierter thermischer Nachbehandlung zu integrieren. Anschließend wird der Strukturdruckprozess fortgesetzt, um das intelligente Bauteil fertigzustellen.
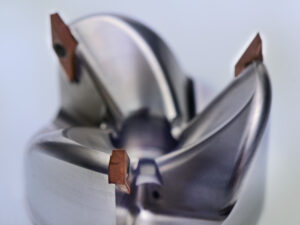
Der Druckprozess wird nach der Integration des Sensors fortgesetzt, um das intelligente Bauteil fertigzustellen. Bild: Fraunhofer ILT
Durch die Kombination von Struktur- und Funktionsdruck sowie laserbasierter Nachbehandlung lassen sich Bauteile mit integrierter Sensorik somit vollständig additiv herstellen. Dies ermöglicht nicht nur die präzise Platzierung von Sensoren für anspruchsvolle Zustandsanalysen, sondern auch den Schutz dieser Sensoren vor mechanischen Umwelteinflüssen. „Die Geometrie der Sensoren kann je nach Bauteil individuell angepasst werden, und zukünftig sind sogar weitere Funktionselemente wie integrierte Heizer denkbar“, erläutert Fink. Nach Auffassung der Forschenden wird diese Technologie vielfältige Anwendungsmöglichkeiten eröffnen: von der Fertigung in den Bereichen Werkzeug- und Maschinenbau bis hin zur Automobilindustrie und darüber hinaus in den Sektoren Energie, Luft- und Raumfahrttechnik.
Quelle und Bild: www.ilt.fraunhofer.de